
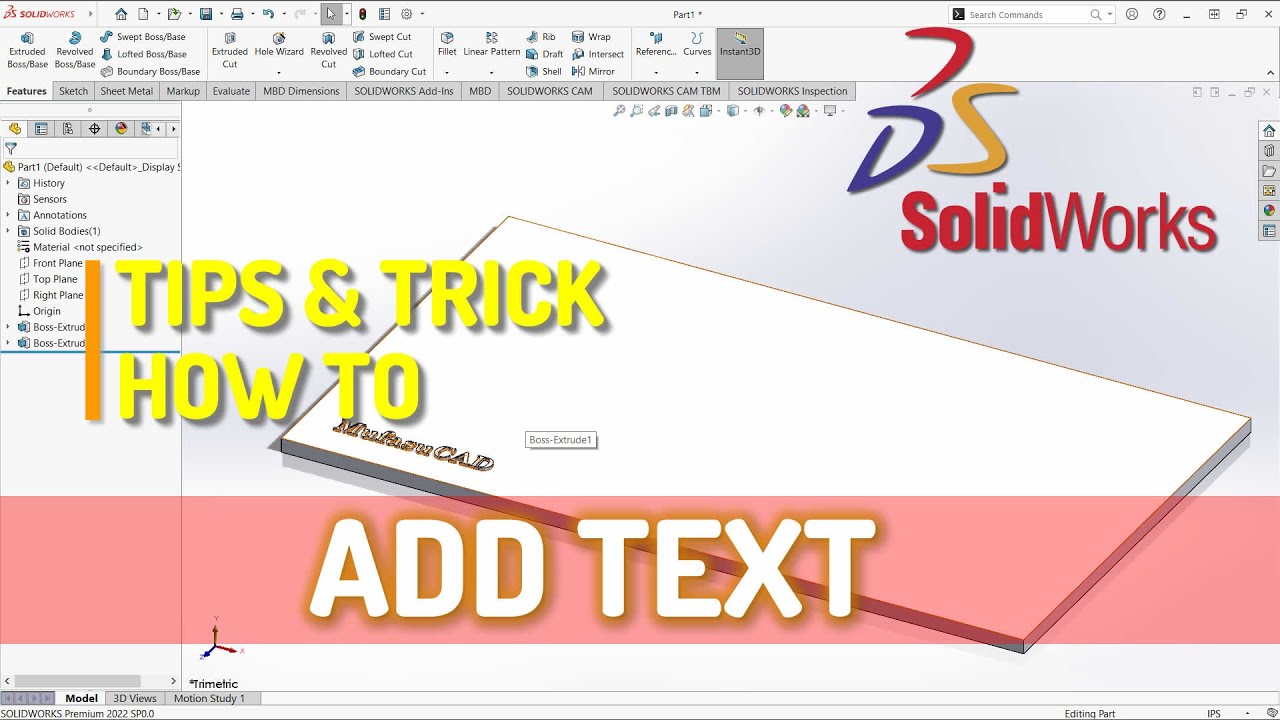
This mechanism acts like a hydraulic shock absorber to soften the impact of opening and closing the valves during operation. Internally, the lifter features an oil reservoir and piston (actuated by the pushrod). Working with the angle ground into the cam lobe, the combination provides preload on the cam (to keep it from walking forward). Externally, the hydraulic flat tappet lifter appears to have a flat mating surface (where it contacts the cam), but the surface is actually crowned. Though simple in appearance, the hydraulic lifter is actually quite complex in design. The lifter’s job is to ride on the cam and (working with the pushrod and rocker) actuate the valve. Toss in the added benefit of a set-it-and-forget-it valve adjustment procedure that eliminated periodic maintenance and whisper-quiet operation, and you can see why hydraulic flat tappet cams continue to be so popular.īefore getting to the next three cam types, we need to take a look at the inner workings of a lifter. Stuffed in a lightweight Chevy II, the L79 was a force to be reckoned with on the street.
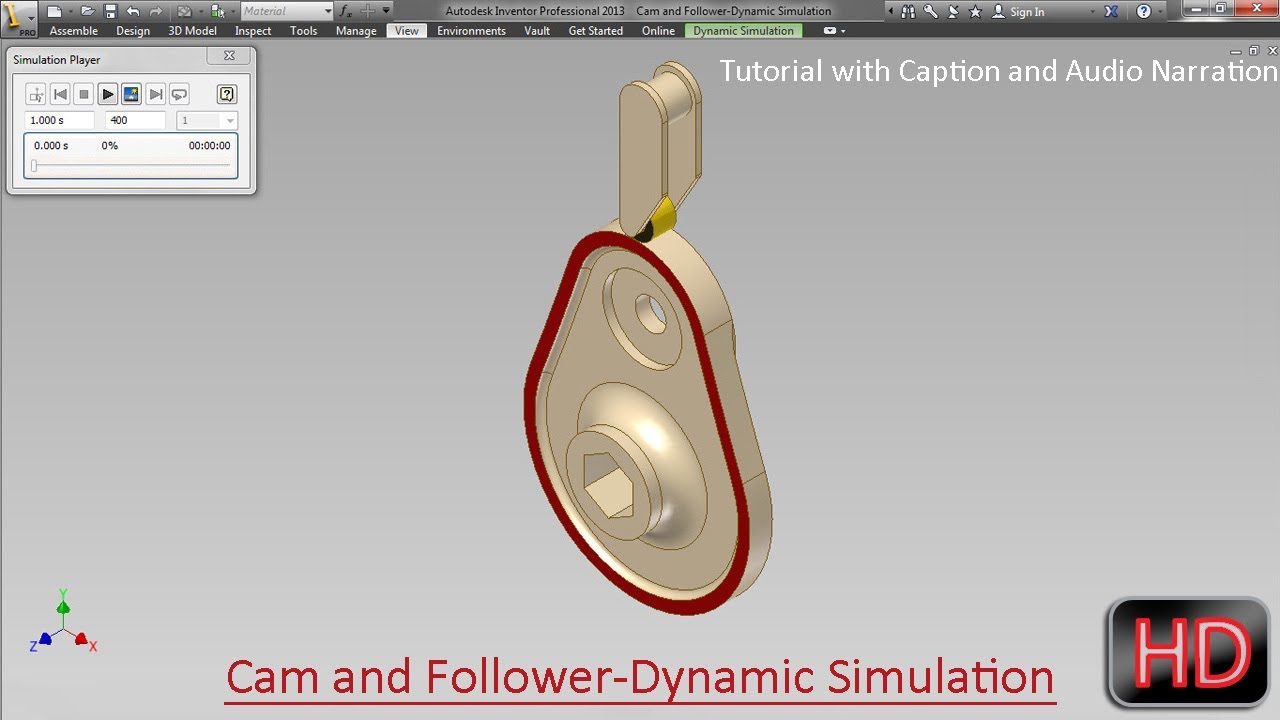
Ask anyone who ever drove the 350hp L79 327 or the 350hp L46 350 how well the hydraulic cammed engines ran. The hydraulic flat tappet cam was used for not only all of the low- (base model) and medium-performance applications, but also made an appearance in a couple of powerful small-blocks in the muscle car era. From a purely cost standpoint, when you produce millions of cams, even a small cost savings starts to multiply very rapidly. Looking at the benefits, it should come as no surprise that the OEMs chose to use the hydraulic flat tappet design for their production vehicles. Used in literally millions of production Chevy big- and small-blocks, to say nothing of the many V-6 applications, the benefits of the hydraulic flat tappet cam includes low cost, minimal maintenance, and the elimination of valvetrain noise. We begin our discussion with the most common cam type offered: the hydraulic flat tappet.
